“The time, the time, who’s got the time?” asked March Hare
Scene from Alice in Wonderland
Do you ever feel like you’re in Wonderland and your watch is two days slow? One of the most important resources within IT is time. We “are too busy resolving incidents to document adequately”, “have no time to complete changes/projects properly”, “have no time to improve” or we “have to test less to meet delivery dates”.
Time is a precious resource, use it wisely
This article presents the notion that time is a precious resource and should be used wisely. That is, stop doing things that don’t add value. See how to measure, learn and improve your use of time to create real value for competitive advantage.
We don’t have time to save time, to save time
Since IT is primarily “Knowledge Work” it’s critical we understand our productivity. Time is the key factor in calculating productivity. It is also important to know what value-added vs. non-value activities consume our time. This implies we must have good measurements in place in order to learn from feedback and improve. And there’s the rub, “we don’t have time to save time, to save time”. Sung to the tune of “There’s a hole in my Bucket”.
This is where Lean IT can help. Lean makes the best of scarce resources like time.
This watch is full of wheels, let’s fix it
You may recall the Mad Hatter tried to fix the White Rabbit’s two day slow watch. He examined it and found it full of wheels. So he replaced them with spoons, butter, jam, sugar and tea. Unfortunately he created a Mad Watch which was promptly stopped by the March Hare with a mallet as it spun out of control. Without the right measures to learn from, we sometimes jump to the wrong conclusions and must start again.
This is where Six Sigma tools can help. Six Sigma is the disciplined and analytical approach for eliminating variation.
Use measurements to learn, improve and create real value
IT Service Management has come a long way in improving how IT systems are being built, deployed and managed.
But when you don’t have enough time, things tend to suffer. We’re pulled in many directions, we cut corners and we lose focus on what’s important in creating real value. We certainly don’t have time to stop and measure where we spend our time.
And there’s the conundrum. It’s tough to effectively manage what we don’t measure. This is called “managing by the seat of your pants” which is risky at best.
Having the right measurements in place helps us learn more quickly through feedback and make better decisions on necessary improvements that keep us laser focused on value creation.
They help to:
- validate, direct, intervene and justify
- concentrate on what’s important
- spot danger in time to correct it
- provide the instrumentation for management control
- analyze, troubleshoot, predict and prevent
- determine root cause and corrective actions
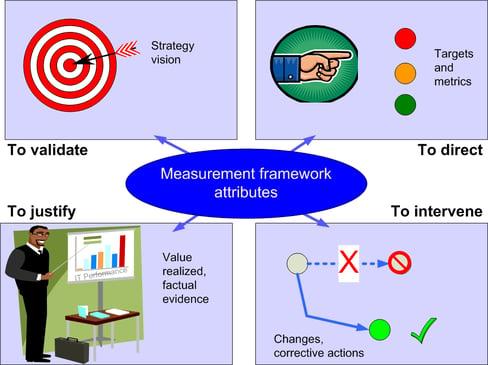
Common measurement challenges
There are three common measurement constraints:
- What to measure. Strategic measurements are not clearly specified and/or do not adequately support value creation. Tactical measurements (text-book) are fuzzy in their support of aligned management targets and objectives. Operational metrics focus on speeds/feeds and are not often associated with tactical or strategic measures.
- Interpreting results. Many lack the skills and methods required to analyze metrics data to support corrective or preventative action. Reactive and proactive techniques are often mismatched or misused. For many, analysis is a dark art, reports and data are not acted on.
- Getting/trusting data. Underlying data collections systems are not designed to support analytical methods required for management decision making, Data availability, reliability, timeliness, gaps, precision, accuracy and slim documentation can create trust issues. This hinders analysis and renders the measurements less than useful.
Overcoming measurement constraints
To address the first constraint we turn to Lean thinking backed with a measurement framework. Lean focuses on improving IT people, IT processes and information technology in order to deliver more value to its customers. We apply the guiding principles of Lean to measuring what matters most “value streams”. The measurement framework ensures the right control measures; so what’s measured gets managed!
“Lean IT is the extension of lean manufacturing and lean services principles to the development and management of information technology products and services. Its goal is to continuously improve the value delivered by IT organizations to their customers and the professionalism of IT people.” Lean IT Association
Six Sigma is our recipe for dealing with the second constraint. Six Sigma seeks to improve the quality of process/service outputs by identifying and removing the causes of defects (errors) and minimizing variability. It makes very good use of statistical and analytical tools to get to the root-cause by using effective problem analysis techniques.
“Six Sigma” is a process improvement set of tools and strategies, originally developed by Motorola in 1986. Six Sigma became well known after Jack Welch made it a central focus of his business strategy at General Electric in 1995 and today it is used in different sectors of industry. Wikipedia
Finally we use scorecard designer software to resolve the third constraint. Scorecard designer software helps reduce the amount of time and effort required to design, deploy and manage your measurements to capture trustworthy data. It is based on customizable templates for rapid development and deployment.
Learn how to use measurements to create real value
Targeted education serves to meet the specific needs of the various levels of IT Service Management.
- The Value Stream educates managers on how to ensure they are measuring what’s important in a coherent and structured approach that is aligned to realize value driven goals using Lean IT measurements.
- The Analytics Stream educates practitioners on how to manage the measurement lifecycle using a repeatable process to drive continual service improvements (CSI); and learn Six Sigma techniques, skills and methods needed to analyze ITSM metrics to support corrective and/or preventative actions.
- The Measurement Stream educates administrators on how to administer the measurement framework to gather metrics for ITSM, process and report meaningful and trustworthy management information.
Let us help you create real value
We know you’re pressed for time. Let our experts help you measure, learn, improve and create real value for competitive advantage.
Step 1 - get free stuff
Step 2 - get tools
Step 3 - get educated
Step 4 - get going
David Smith is the president of Micromation Inc. We help organizations increase customer value through continual improvement of services and processes by minimizing waste while maximizing yield.
David is the author of “Implementing Metrics for IT Service Management” ISBN: 9789087531140 and contributing co-author of "IT Service Management - Global Best Practices" ISBN: 9789087531003.